When you’re looking for ways to improve a process, the boardroom may not be the best place to begin. It’s easy to overlook some important detail when you’re considering a process in an abstract way.
Toyota realized this and incorporated the Gemba Walk into its Lean and Six Sigma philosophies. And as you probably know, businesses all over the world have benefited from implementing Lean and Six Sigma. So, what is a Gemba Walk, and how can you get it working for you?
The word “Gemba” is Japanese for “the real place.” Visiting the real places where your business generates value is what the Gemba Walk is all about. In practice, it means spending time watching processes in action and asking people who are at the coalface questions about the work they do. The information you gather during a Gemba walk serves as the basis for your process improvement initiative.
Although the Gemba Walk was developed in a manufacturing context, it applies to any type of process. So, even if you’re in a service industry, it’s worth taking a closer look at how your team navigates processes.
How the Gemba Walk Works
Walking around looking at things and asking questions may sound simple, but in order to get the best value for your time, you need to follow a systematic process yourself.
1. Prepare for the Gemba Walk
Although one person can do a Gemba Walk on his or her own, especially in smaller businesses, it’s best to have a small team to help you get the full picture from a variety of perspectives. What you miss, another team member may notice, or perhaps you notice the same things but focus in on different details.
Who should you consider including in your team? Consider these people as potential Gemba Walk team members:
- A manager who is relatively unfamiliar with the process you’re studying. He or she will have fewer preconceived ideas and will give you the fresh perspective you need.
- A supplier whose equipment or materials are used in the process. You will have the benefit of technical knowledge you don’t have. Is your equipment being used correctly? Are your materials being used efficiently? Your supplier may have valuable input to give.
- A customer may not be your number one choice for a Gemba Walk team but consider it nonetheless. What you think your customers want and what they value could be two different things.
- A sales representative has direct contact with customers and knows what they want. Besides giving input, it will also help your sales representatives to see how value is created.
2. Prepare Your Staff for Your Gemba Walk
You don’t want the team or teams under observation to feel uncomfortable with the Gemba Walk, so they need to know what you’re trying to achieve. Make sure they understand that a Gemba Walk aims to collect information that could make their jobs easier. It’s not about people and their individual performance. Instead, it’s about processes and making them more efficient for the good of all concerned.
When you brief your staff on the Gemba Walk, ask for suggestions. The people who physically do the work involved will often have the best insight into problem areas they’d like you to attend to. Asking for input and being receptive to the feedback you get helps your staff to feel that their opinions are of value and increases their engagement in the process improvement drive.
Essentially, the message you’re trying to get across is: “We’re taking a new look at an old process and as we do this, we’re going to ask you a bunch of questions. There are no wrong answers. Feel free to respond honestly. We’re not here to criticise you or your work, and your contribution to what we’re trying to achieve will be valued.”
3. Know What You Want to Achieve
“Process improvement” is a very broad term. What, precisely, are you hoping to achieve? For example, you may want to:
- Find ways to save time
- Address quality issues
- Reduce costs
- Improve workplace safety
- Reduce any of the seven wastes of Lean
- Improve service and customer experience
4. Know That Gemba isn’t MBWA
Because both activities involve walkabouts, managers often get confused between Gemba Walks and Management by Walking About (MBWA). However, there are fundamental differences between the two. MBWA is much less focused, and it doesn’t involve the in-depth observation and open-ended questioning that form a fundamental part of the Gemba Walk process.
If this sounds a little intimidating, don’t worry. You don’t have to acquire the expertise of every person whose role in the process falls under observation. Instead, you will rely on the people doing the work to share their insights and expert opinions on the work they do. Asking the right questions will get you this information, and we’ll look at this aspect of the Gemba Walk shortly.
5. Follow Your Value Chain from Beginning to End
There’s no better way to observe a process than following it from the point where your business springs into action all the way through to a finished product or service delivery.
Transfer time, the time it takes for your teams or employees to hand over to the next team or employee, and queue time after handover are often fertile ground for process improvement. The best way to spot bottlenecks or delays in a process is to follow it from start to finish.
6. Remain Focussed on the Process
Now that you’ve planned your route and have prepared yourself and your staff, your Gemba Walk begins. Remember, you’ve told your people that you’re not there to criticize them or their work. You are not gathering data for a personnel performance evaluation. Keep this firmly in mind.
This can be hard to do when you notice Johnny slacking off at the coffee machine, or catch Jenny messing around with her smartphone when she would be working. But if you intimidate your employees by finding fault, you’ve lost their engagement and can’t expect them to be open to you when questioned.
Some of the answers to your questions may not be what you want to hear, but again, the Gemba Walk isn’t the time to pass judgment on your employees, their opinions, or how you perceive their attitude. Remain focused on the process.
7. Ask the Right Questions
Remember that you are taking a fresh look at a process. Putting aside your preconceived ideas on what to do, how to do it, and when to do it may be hard to do, but it’s exactly what you should do. Some companies find this so difficult that they employ consultants to do the Gemba Walk. If you’re doing it yourself, try to approach it as if you knew absolutely nothing about the business process you’re investigating.
You may also find that the people engaged in a process have unofficially tweaked it for one reason or another. So, even if you think you’re up to speed with how a process is performed, try to forget this knowledge. Keep an open mind and don’t tackle any people performance issues you think you’ve identified.
All your questions should be open-ended. Questions that require “yes” or “no” answers, are out. Instead, you want people to elaborate. To get answers that will make your Gemba Walk effective, ask questions using the 5 W’s.
Who?
- Who is involved in this part of the process?
- Who sets the work in motion?
- Which role does which task?
- Who else can do it?
- Who should do it?
- Who will take over when this part of the process is complete?
Note: “Who” is a people word. Beware of asking who should be blamed for any problems you pick up!
What?
- What inputs do you receive?
- What do you do with them?
- What could or should be done instead?
- What outputs are you expected to deliver?
- What factors cause delays or waste?
Note: “How” questions are also open-ended, and if you think they will help to clarify the “What” questions, feel free to add some.
Where?
- Where do materials or other inputs come from?
- Where is the work performed?
- Where else could it or should it be done?
- Where do your outputs go?
- Where are tools and equipment located?
Note: Movement doesn’t add value, and it takes time, so you want to limit this as much as possible. Small changes can make a big difference. Save a second, and you just saved that time multiplied by however many times the employee performs that portion of a task.
When?
- When do you receive process inputs?
- When would be the best time to receive them?
- When do you find yourself waiting for something you need?
- When are you able to begin working on turning inputs into outputs (queue time)?
- When is your work complete?
- When you have completed your part of the process, how do you hand it over to the next staff member or department?
- When does the next sub-process begin?
Why?
- Why do we perform this step or sub-step?
- Why do you do this portion of the task?
- Why perform tasks in this specific order?
- Why is it important to our customers?
8. Log Your Observations
Your Gemba Walk will produce a large amount of information. In retrospect, you may find that observations that seemed trivial at the time impact on your process improvement strategy. Recording observations electronically is helpful because you and your team can share them, collate them, and decide where action is required. But even jotted-down pen and paper notes will be more helpful than nothing at all.
You aren’t going to even try analyzing the data you collect on a Gemba Walk and turning it into actions until after you’ve seen the whole picture. By that time, you could have forgotten crucial details. You and your team’s notes are therefore extremely valuable to the Gemba Walk’s success.
A camera can also be helpful. For instance, if you notice that there is redundant equipment that gets in the way, or if you observe that equipment layouts could be improved, you can link photographs to notes when trying to resolve the issue. Video is likewise useful on occasion.
9. Never Base Findings on Assumptions
If ten people do the same job, they can still do it in ten different ways. And even if you think there’s a cast-in-stone process methodology, people may have adapted it or interpreted it differently to you. An open mind is a prerequisite for a Gemba Walk. Assumptions are not facts. Get the facts.
10. Never Start Implementing Changes During a Gemba Walk
By all means, collect suggestions from employees, but never make any decisions or try to implement any changes right away. You first need the big picture. Then you need time to consider it carefully. What looks like a great idea for process improvement when you’re visiting sub-process one may not seem like such a good idea once you’ve reached sub-process ten.
Changing processes should never be done on an ad-hoc basis. You may find that there are unexpected impacts you didn’t take into account.
11. Give Your Employees Feedback
Before and during your Gemba Walk, you Employees gave their insights and suggestions. They deserve feedback even if you aren’t planning to make a single change. Whether you call a general meeting or send feedback in the form of a report or an electronic message, your teams will want to know what your findings were.
Although they may not have been among your Gemba Walk analysts or observers, your employees certainly took part in the process. Remember to give recognition to those who were free with information, suggestions, and opinions. Explain why certain changes were adopted, and if you decided not to implement certain suggestions, give the reasons you chose not to do so.
12. Follow up With Subsequent Gemba Walks
You’ve made changes to processes, but how effective are those changes? Your stats might look good, but stats can be misleading. Maybe you haven’t achieved the results you wanted after all. Why don’t you see your projected results? The only way to know is to follow up, and since you’re working with practical realities rather than abstract theories, another Gemba walk is in order.
Alternatively, you didn’t spot anything that needed change, but is your process really perfect? Are processes still happening in the same way as they did before? Once again, a new Gemba Walk will help to provide you with the insights you need to answer these questions.
Beyond the Gemba Walk: Improving Your Processes
Knowing what you want to change in your business processes is a good start. The data you gathered in your Gemba walk will indicate what processes need to be redesigned or adjusted. Now, the real work begins.
How will you go about business process improvements? Once you’ve decided that, how will you capture, communicate, and implement the changes that you want to make? And given that change management is a delicate process, how will you go about making sure the changes are implemented with the minimum of hitches?
It’s not as simple as just revisiting the process areas you chose to improve your Gemba walk. Adjacent sub-processes may be impacted by your adjustments, and different, but related processes, could get into hot water too. For example, a change to a production process could affect the sales process, and you need to be on top of your game to deal with any worrying symptoms there.
At this point, you might feel as if you need to be omniscient. Is all of this humanly possible? Luckily, you don’t need supernatural abilities to design, test, and implement changes.
1.Know where the Problem Areas Are
You can analyze all your process flows using workflow software. For example, Tallyfy, a cloud-based process-flow solution, can help you to capture entire processes, implement them and analyze them at a glance.
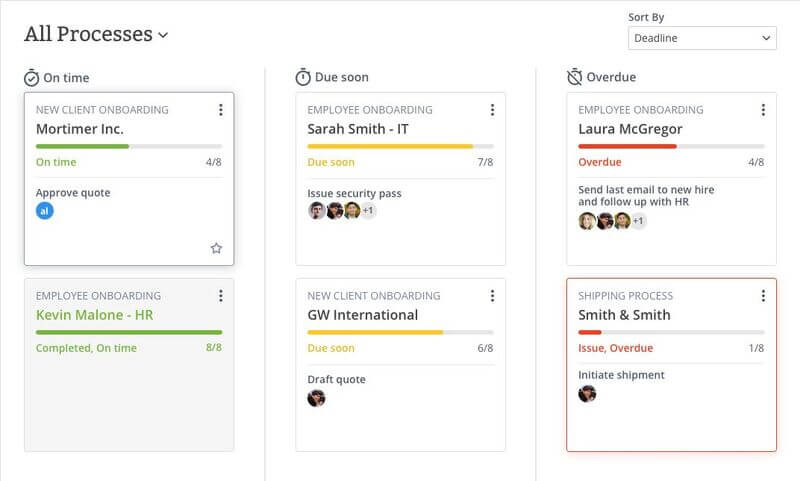
Dashboard showing current, pending, and overdue portions of processes. In this example, shipping indicates a problem area
Where are the delays? How does each task flow into the next? Although you won’t have any preconceived ideas when undertaking a Gemba Walk, knowing what you want to improve and where you need to intervene once you’ve made those changes is the first step towards achieving a valuable result.
2. Model Possible Solutions
You don’t need to dive into implementation head-first and hope for the best. Use the same software to model ideas for process improvement before implementation. How will your changes impact elsewhere in the process? Do the changes you have in mind address the problems you identified? How do they impact on other processes in your business? Yes, a model isn’t the same as a reality, but it does indicate whether there are any serious gaps in your plan.
3. Test Them in Real-Life Conditions
Now that you’re happy with the model, it’s time to see whether your process improvement strategies work in real life. The time when an organization switches process flows is particularly delicate. Staff members need to understand your new process flow and their role in it. Managers need to be alert to queries, problems, and obstacles.
Tallyfy offers a way to issue instructions, remind employees of the methods and standards they now need to conform to and gives them a platform for reporting problems or delays.
Gemba Walks and Software Tools: A Powerful Combination
Gemba Walks give you new insights into how your organization navigates processes and where problems lie. The software can do that to a certain extent too, but what it can’t do is to observe as the human eye observes. For example, if a workstation’s layout is inefficient, software can’t report on that or make suggestions for improvement.
It’s highly unlikely that technology will ever be able to replace the Gemba Walk, but it can help you to find direction, test possible solutions, implement them, and monitor their implementation with much greater efficiency. It can also help you with communication and real-time troubleshooting.
Together, the Gemba Walk and Tallyfy can help you to achieve the process efficiencies you always wanted for your organization, sharpening your competitive edge, and boosting your bottom line.