“The secret of getting ahead is getting started. The secret of getting started is breaking your complex overwhelming problems into small manageable tasks, and starting on the first one.”
– Mark Twain
- Continuous improvement isn’t about massive overhauls—it’s about making work 1% better each day. Companies using structured continuous improvement see 23% higher profitability and 12% better customer satisfaction scores according to McKinsey’s 2024 operations research.
- The real magic happens when frontline workers—the ones actually doing the work—can suggest improvements right where problems occur. Manufacturing companies report 40% faster problem resolution when workers can flag issues directly in their workflow tools.
- Most improvement programs fail because they’re too complex or theoretical. What works? Simple feedback loops, visible progress tracking, and celebrating small wins. One logistics company reduced delivery errors by 67% just by letting drivers comment on route problems.
- Ever wonder how mid-size companies actually track improvements without drowning in spreadsheets? Maybe it’s time to explore how modern teams make continuous improvement visible and measurable—let’s chat about what’s working for others in your industry.
Here’s something nobody talks about: your best employees probably spend 2.5 hours every single day just hunting for information, updating spreadsheets, or sitting in meetings about meetings. That’s not an exaggeration—it’s from Asana’s 2024 Anatomy of Work report studying 10,000+ knowledge workers.
Meanwhile, companies talk endlessly about “transformation” and “innovation” while their teams drown in broken processes that nobody’s bothered fixing for years.
Sound familiar?
The truth is, you don’t need another massive digital transformation project. You need continuous improvement—the unsexy but incredibly effective practice of making things slightly better every single day.
What continuous improvement really means (hint: it’s not what consultants tell you)
Forget the corporate jargon for a second. Continuous improvement is stupidly simple: it’s fixing the small, annoying problems that make work harder than it needs to be.
You know what I’m talking about.
That approval process that takes 5 days when it should take 5 hours. The customer onboarding that requires 14 different handoffs. The monthly report that three different people create because nobody knows who actually owns it.
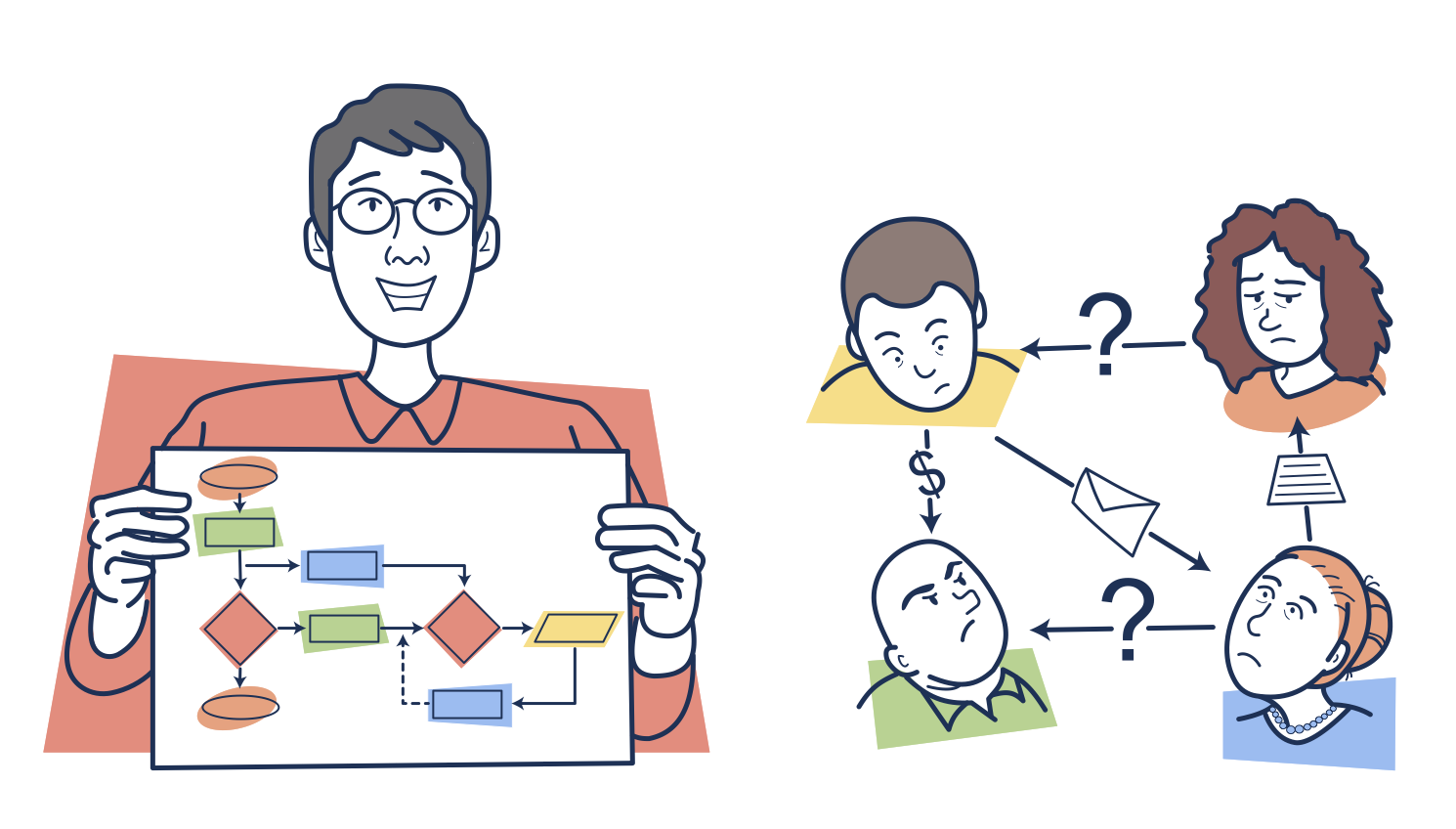
The eternal struggle: what processes look like on paper versus Monday morning reality
Real continuous improvement means two things that most companies get completely wrong:
1. It’s about small wins, not moonshots
Amazon didn’t become Amazon overnight. They started by making book delivery 1% faster. Then payment processing 1% easier. Then returns 1% simpler. Twenty years and thousands of tiny improvements later, they’re delivering packages with drones.
A mid-size healthcare company in Ohio reduced patient wait times from 47 minutes to 19 minutes over six months. How? By fixing one small bottleneck every week. First, they digitized intake forms (saved 3 minutes). Then they staggered appointment scheduling (saved 5 minutes). Then they created a triage system for common issues (saved 8 more minutes).
Each change? Tiny. The cumulative impact? Massive.
2. Your frontline workers know more than management
This one hurts, but it’s true.
The person processing invoices all day knows exactly why payments are delayed. The customer service rep knows precisely which policies frustrate clients. The warehouse worker knows why orders get picked wrong.
Yet most companies have “improvement committees” full of executives who haven’t done actual work in years. No wonder 70% of change initiatives fail (that’s from McKinsey, not me making numbers up).
Smart companies flip this completely. They create systems where anyone can suggest improvements right where they work, without filling out some ridiculous form or waiting for the quarterly planning meeting.
The hidden costs of not improving (warning: these numbers will annoy you)
Let’s talk money, because that’s what gets executives to actually pay attention.
IDC research found that Fortune 500 companies lose $31.5 billion annually due to inefficiencies. Not from big disasters—from tiny, fixable problems that compound over time.
Here’s what that looks like at human scale:
- Knowledge workers waste 2.5 hours daily on duplicate work and information hunting (Asana, 2024)
- Managers spend 23 hours weekly in meetings, half of which are unnecessary (Doodle, 2023)
- 60% of employees have never received feedback on process improvements they’ve suggested (Gallup, 2023)
- Companies lose 20-30% of revenue every year due to inefficiencies (IDC)
But here’s the kicker: fixing these problems isn’t expensive or complex. A financial services firm in Dallas saved $1.2 million annually just by creating a simple system for employees to report and fix process problems.
Why most continuous improvement programs fail spectacularly
Let me guess—your company tried Six Sigma and it fizzled out. Or you hired consultants who left behind a 200-page “transformation roadmap” that nobody’s opened since.
You’re not alone. MIT research shows that 60-70% of continuous improvement initiatives fail within two years.
Why? Three reasons nobody wants to admit:
Reason 1: Death by methodology
Companies get obsessed with frameworks—Lean, Six Sigma, Kaizen, TQM, Agile. They spend months training people on DMAIC and value stream mapping while actual problems go unfixed.
It’s like learning the technical specs of a hammer while your house falls apart.
One manufacturing company spent $400,000 on Six Sigma black belt training. Result? Zero measurable improvement. Why? They forgot to actually give people time and tools to implement changes.
Reason 2: The Excel nightmare
You know what kills improvement faster than anything? Tracking it in spreadsheets.
First someone creates a “master tracking sheet.” Then departments create their own versions. Soon you’ve got 47 different Excel files, none of which sync, half of which are out of date, and nobody knows which one is the “real” version.
Sound familiar? That’s every company I’ve ever worked with.
Reason 3: No visibility, no accountability
Here’s a fun experiment: ask five people in your company what improvement projects are currently running. I guarantee you’ll get five different answers.
When improvements aren’t visible, they don’t happen. When nobody’s accountable, nothing changes. When progress isn’t celebrated, people stop trying.
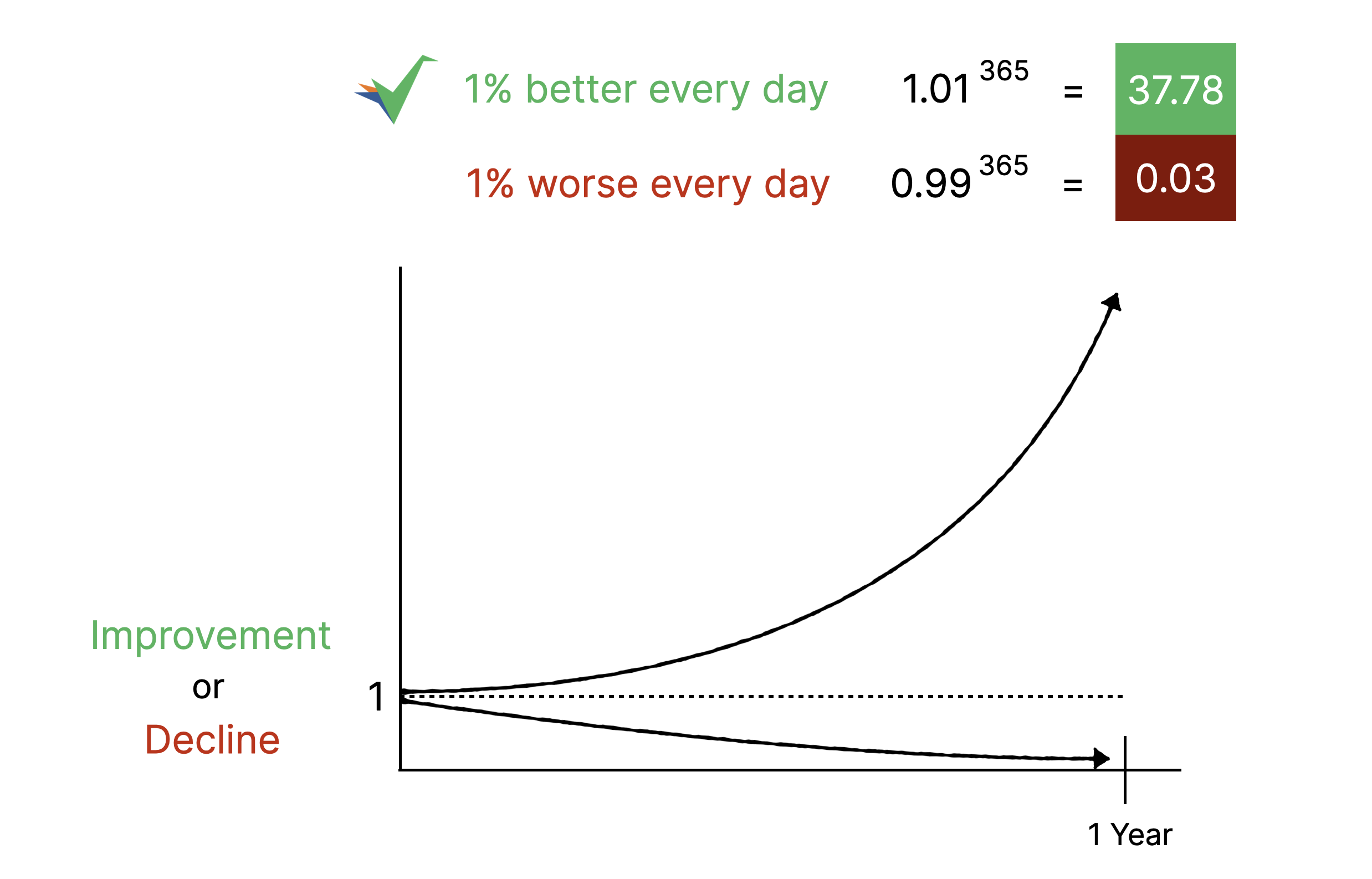
Small improvements compound: 1% better daily = 37x better in a year
What actually works: continuous improvement for normal humans
After watching hundreds of companies try and fail at this, here’s what actually works in the real world:
Start with the problems people complain about most
You know that thing everyone grumbles about at lunch? Fix that first.
A software company in Austin had a running joke about their expense approval process taking “somewhere between 2 days and 2 centuries.” They fixed it in one afternoon by setting up automatic routing based on amount thresholds. Approvals now take 4 hours maximum.
The lesson? Start where the pain is obvious.
Make feedback ridiculously easy
If someone has to fill out a form, schedule a meeting, or “submit a proposal” to suggest an improvement, it won’t happen.
What works? Let people flag issues right where they encounter them. Customer service rep notices a policy causes confusion? They comment directly on that step in the process. Warehouse worker sees a safety issue? They flag it immediately with a photo.
No forms. No committees. Just “hey, this is broken, here’s how to fix it.”
Implement the 24-hour rule
When someone suggests an improvement, respond within 24 hours. Not necessarily with a solution, but with acknowledgment and next steps.
“Thanks Sarah, that’s a great catch about the duplicate approval step. I’ll review with the team Tuesday and let you know what we can do.”
Simple, right? Yet 60% of employees say their suggestions disappear into a black hole. No wonder they stop suggesting things.
Track three metrics (and only three)
Companies love metrics. They track everything, understand nothing, and improve even less.
Pick three numbers that actually matter:
- Time to complete the process (is it getting faster?)
- Error rate (are mistakes decreasing?)
- Employee/customer satisfaction (are people happier?)
That’s it. A logistics company in Memphis improved on-time delivery from 87% to 96% by tracking just these three things for their shipping process.
Real examples from companies that don’t have unlimited budgets
Let’s look at how mid-size companies—the ones without Google’s resources—actually do this:
The dental practice that cut patient wait time by 64%
A 12-location dental practice in Florida had a problem: patients waited an average of 31 minutes past their appointment time. They tried everything—hiring more staff, extending hours, threatening dentists with consequences.
Nothing worked.
Then they tried something different. They gave each receptionist the ability to document and suggest improvements to the scheduling template. Within 3 months:
- Discovered that certain procedures always ran over (adjusted scheduling blocks)
- Found that Mondays had 40% no-show rates (started confirmation calls on Fridays)
- Realized lunch scheduling created afternoon bottlenecks (staggered lunch breaks)
Result? Average wait time dropped to 11 minutes. Patient satisfaction scores jumped 34%. No new hires, no expensive consultants, just frontline workers fixing what they saw broken.
The manufacturer that eliminated 95% of documentation errors
A medical device manufacturer in Minnesota was drowning in FDA compliance issues. Their documentation error rate was 8.3%—each error potentially meant regulatory fines.
Their solution wasn’t more training or stricter policies. They built simple checklist templates that guided workers through compliance requirements step by step, with automatic verification at each stage.
Workers could flag confusing steps directly in the workflow. Within 6 months, documentation errors dropped to 0.4%. FDA audits that used to take weeks now finish in days.
The retailer that turned complaints into improvements
A regional clothing retailer with 43 stores had a problem every retailer knows: returns. Their return rate was 18%, way above the industry average of 10%.
Instead of tightening return policies (which just annoys customers), they did something clever. They created a simple feedback loop where store associates could tag return reasons and suggest fixes.
The insights were goldmine:
- “Size charts are confusing” → Updated all online size guides with actual measurements
- “Colors look different online” → Added multiple angle photos and “true color” notes
- “Fabric feels cheap” → Removed three underperforming suppliers
Return rate dropped to 11% in one year. Customer lifetime value increased 23%.
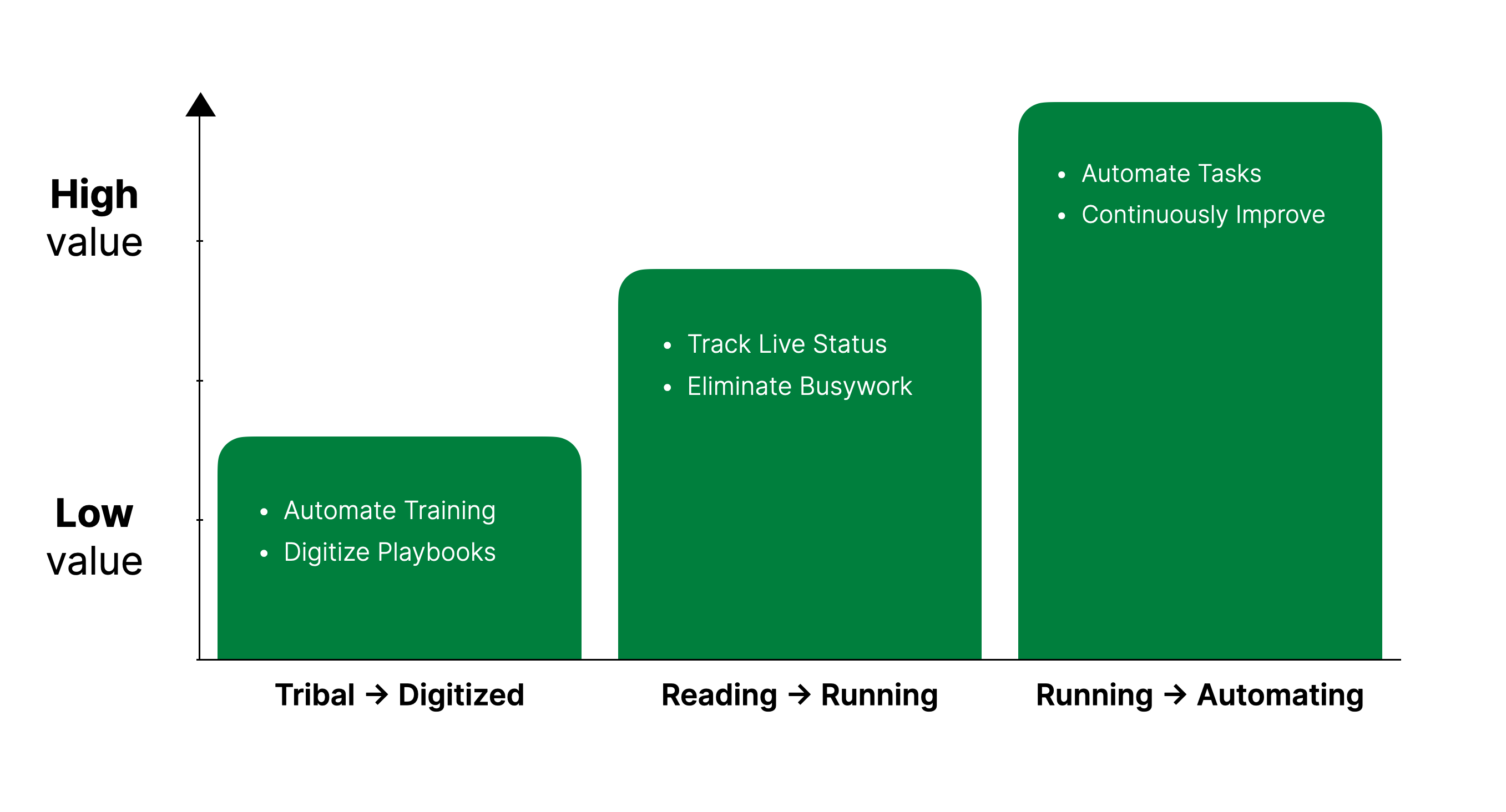
The transformation journey: from manual chaos to systematic improvement
The tools that actually matter (spoiler: it’s not about the tools)
Everyone wants to know about tools and software. Here’s the truth: continuous improvement is 80% culture and 20% tools. But that 20% matters when you’re scaling beyond sticky notes.
What doesn’t work
Spreadsheets: Great for analysis, terrible for collaboration. By the time your Excel file makes it around the team, it’s outdated.
Project management tools: Trello, Asana, Monday—they’re built for projects, not processes. You’ll spend more time updating boards than improving anything.
Email: Where good ideas go to die. “I’ll review this and get back to you” = “This will never happen.”
What actually works
You need three things:
- Process visibility: Everyone should see how work actually flows, not how it’s supposed to flow
- In-context feedback:Workers need to comment directly on process steps, not in separate systems
- Automatic tracking: If people have to manually update progress, it won’t happen
A marketing agency in Seattle replaced their 47-tab Excel monster with a simple workflow system where team members could see every process, suggest improvements inline, and track results automatically. Time to launch campaigns dropped from 3 weeks to 8 days.
The psychology of improvement (or why humans resist change)
Here’s what nobody tells you about continuous improvement: the biggest obstacle isn’t technology or methodology. It’s human psychology.
People hate change. Even positive change. It’s literally wired into our brains—the amygdala treats any change as a potential threat.
So how do you overcome this?
Make the first change tiny and unscary
Don’t start by revolutionizing the entire order fulfillment process. Start by fixing the label printer that jams every Tuesday.
A insurance company in Phoenix wanted to digitize their entire claims process. Instead of a big bang approach, they started with one thing: letting adjusters upload photos from their phones instead of emailing them later. Tiny change, huge time savings, zero resistance.
Once people saw it worked, they asked for more improvements.
Celebrate improvements like victories
When someone’s suggestion saves 10 minutes per day, make a big deal about it. Send a company email. Mention it in the all-hands. Give them a $50 gift card.
Yes, it feels cheesy. Do it anyway.
A distribution center in New Jersey created an “Improvement Wall” where they posted every implemented suggestion with the person’s photo. Suggestions increased 400% in three months.
Make failure safe
Half of improvements won’t work. That’s fine. Actually, it’s better than fine—it means people are trying.
Create a “Failed Forward” culture where unsuccessful improvements are learning opportunities, not career limitations. “We tried automatic scheduling but it didn’t work because of X. Now we know to focus on Y instead.”
How to start tomorrow (literally, tomorrow)
Enough theory. Here’s exactly what to do:
Day 1: Pick your most painful process
Ask 10 people: “What process wastes the most time around here?”
Whatever gets mentioned most, that’s your starting point. For a tech company I worked with, it was employee onboarding. For a hospital, it was discharge procedures. For a manufacturer, it was inventory counts.
Pick one. Just one.
Week 1: Map what actually happens
Not what the manual says. Not what should happen. What actually happens.
Document every step, every handoff, every place where things get stuck. Use whatever tool you want—whiteboard, sticky notes, or actual workflow software. Just make it visible.
You’ll discover at least three things that make you say “wait, we do WHAT?”
Week 2: Ask the people doing the work
Sit with the people who actually run this process every day. Ask three questions:
- What part of this process makes you want to scream?
- If you could fix one thing, what would it be?
- What would make this easier for customers/other departments?
Write down everything. Judge nothing.
Week 3: Fix the easiest thing first
Look at your list of problems. Find the one that’s easiest to fix. Not the most important, not the most visible—the easiest.
Fix it.
A restaurant chain fixed their inventory problem by… moving the clipboard three feet closer to the freezer. Saved 20 minutes per day per location. Sometimes it’s that simple.
Week 4: Make it systematic
Now here’s where most companies fail—they stop after one improvement.
Don’t do that.
Create a simple rhythm:
- Monday: Review new improvement suggestions
- Wednesday: Update on current improvements
- Friday: Celebrate what got better this week
That’s it. No complex frameworks, no certification programs, just consistent focus on getting better.
The metrics that prove it’s working
How do you know if continuous improvement is actually working? Track these:
Leading indicators (what tells you you’re on track)
- Number of suggestions per employee: Should increase over time as people trust the system
- Time from suggestion to implementation: Should decrease as you get better at improvements
- Participation rate: What percentage of team members have made at least one suggestion?
A call center in Tampa tracks these weekly. When suggestions dropped, they discovered managers weren’t responding to ideas. Fixed that, suggestions tripled.
Lagging indicators (what tells you it worked)
- Process cycle time: How long things take from start to finish
- Error rates: Mistakes, rework, customer complaints
- Cost per transaction: Total cost divided by number of completions
- Customer/employee satisfaction: NPS, CSAT, or simple pulse surveys
Modern workflow tools can track these automatically, but even a simple monthly review beats not tracking at all.
Industry-specific examples that actually apply to you
Let’s get specific about what continuous improvement looks like in different industries:
Healthcare: Beyond the clipboard
A 200-bed hospital in Ohio reduced ER wait times from 3.5 hours to 1.5 hours. How?
- Nurses could flag bottlenecks directly in patient flow systems
- Triage protocols updated based on frontline feedback, not committees
- Created “fast track” for common conditions identified by staff patterns
They didn’t buy new equipment or hire more doctors. They just listened to the people doing the work and made their suggestions visible.
Manufacturing: The 5-minute fix philosophy
An automotive parts manufacturer in Michigan reduced defects by 73% with one rule: any problem that can be fixed in 5 minutes gets fixed immediately.
Machine operator notices a calibration issue? Fix it now, document it later. Quality control spots a labeling problem? Stop the line for 5 minutes, prevent 500 mislabeled parts.
Previously, everything went through a change request process that took weeks. Now, frontline workers have authority to make immediate improvements.
Financial services: Killing the spreadsheet monster
A regional bank with 45 branches had 127 different Excel templates for various processes. Nobody knew which were current. Updates took weeks to propagate.
Solution: They created single-source-of-truth digital processes where tellers could suggest improvements directly. In 6 months:
- Account opening time cut by 40%
- Compliance errors down 89%
- Employee satisfaction up 31%
The key? Branch employees could see and suggest improvements to processes in real-time, not through quarterly reviews.
Professional services: Escaping email hell
A consulting firm with 150 employees calculated they sent 50,000 internal emails per month. Half were “status updates” that nobody read.
They implemented visible workflow tracking where project status was always clear. Result? Internal emails dropped 70%. Billable hours increased 15% (turns out people work more when they’re not writing emails about work).
The cultural shift that makes it stick
Here’s the uncomfortable truth: continuous improvement isn’t a program you run. It’s how your company operates. Forever.
That requires a fundamental culture shift that most companies aren’t willing to make.
From “that’s how we’ve always done it” to “how can we do it better?”
This is the hardest change. It requires leaders to admit current processes aren’t perfect. It requires managers to accept suggestions from people they manage. It requires everyone to be comfortable with constant change.
A logistics company in Atlanta made this shift by changing one thing: their weekly meetings. Instead of status updates, they discuss “What broke this week and how do we fix it?” Brutal honesty replaced corporate theater.
From individual heroes to systematic excellence
Stop celebrating the person who works until midnight to fix problems. Start celebrating the person who makes problems impossible.
A software company stopped giving “firefighter awards” to people who fixed crises. Instead, they started recognizing “prevention champions” who stopped problems before they started. Crisis incidents dropped 60% in one year.
From perfection paralysis to rapid iteration
Companies spend months planning the perfect improvement. By the time they implement it, the problem has evolved.
Better approach: implement 80% solutions in days, not months. A workflow that’s 80% better today beats one that’s 100% better next year.
Common excuses and why they’re nonsense
I’ve heard every excuse for not doing continuous improvement. They’re all terrible.
“We don’t have time”
You don’t have time NOT to improve. You’re already wasting 2-3 hours daily on inefficiencies. Fixing one process saves more time than it takes.
A accounting firm said they had no time for improvements. They tracked their work for one week: 35% was rework from preventable errors. One afternoon of process improvement saved 10 hours weekly.
“Our processes are too complex”
Complex processes need improvement most. Start with one subprocess. Fix that. Move to the next.
An aerospace manufacturer thought their assembly process was too complex to improve. They started with just the tool checkout procedure. Saved 20 minutes per shift per worker. That’s 100 hours monthly across the facility.
“People won’t adopt changes”
People resist top-down changes. They embrace improvements they suggested themselves.
When employees own the improvements, adoption rates exceed 90%. When management mandates changes, adoption barely hits 30%.
“We need executive buy-in first”
No, you don’t. Start small, show results, then executives will beg to expand it.
A customer service team started tracking and fixing issues without permission. After reducing complaint resolution time by 50%, executives suddenly became very interested in “their” continuous improvement initiative.
What continuous improvement looks like with modern tools
Let’s be practical about technology’s role. You don’t need AI or blockchain or whatever consultants are selling this week.
You need tools that make improvement visible, trackable, and systematic.
Process visibility everyone understands
Your processes should be as clear as Google Maps. Anyone should see where work is, where it’s stuck, and where it’s going.
A property management company replaced their email-and-Excel chaos with visual workflow tracking. Maintenance requests that took 5 days now complete in 1.5 days. Residents can see exactly where their request is, reducing “where’s my repair?” calls by 80%.
Feedback where work happens
Workers shouldn’t leave their work environment to suggest improvements. The feedback mechanism should be built into the work itself.
Think about it: Amazon didn’t create a separate “review website.” They put reviews right on the product page. Your improvement suggestions should be just as integrated.
Analytics that actually matter
Most companies drown in data but starve for insights. You need simple analytics that answer three questions:
- Where are the bottlenecks?
- What’s getting better or worse?
- What should we fix next?
A fulfillment center uses simple dashboards showing cycle time, error rates, and improvement impact. No complex BI tools, just clear visibility into what matters.
The improvement playbook for different company sizes
Small companies (10-50 employees): Keep it simple
You don’t need frameworks or methodologies. You need a weekly standup where people share what’s broken and someone fixes it.
A 30-person marketing agency does “Fix-it Fridays”—last hour of every Friday, the whole team shares one annoying problem and brainstorms solutions. They’ve fixed 150+ issues in two years.
Mid-size companies (50-500 employees): Systematize without bureaucracy
You need structure but not red tape. Create clear ownership for processes, simple feedback channels, and regular improvement rhythms.
A 200-person software company assigns “process owners” who review suggestions weekly and can implement changes without committees. Average time from suggestion to implementation: 6 days.
Large companies (500+ employees): Decentralize improvement
Don’t create a central improvement office. Enable each department to improve their own processes with common tools and principles.
A 2,000-person manufacturer gives each facility budget and authority for improvements under $10,000. Facilities compete for “most improved” quarterly. Company-wide efficiency up 18% in one year.
The questions leaders should ask (but usually don’t)
If you’re in leadership, here are the questions that actually drive continuous improvement:
Instead of “What’s the status?” ask “What’s broken and how can we fix it?”
Instead of “Why did this fail?” ask “What did we learn and what’s our next experiment?”
Instead of “Who’s responsible?” ask “How do we prevent this systematically?”
Instead of “When will it be done?” ask “What’s the smallest improvement we can make today?”
A CEO in Boston changed their weekly leadership meeting to focus only on these questions. Result? 47 process improvements implemented in 6 months versus 3 the previous year.
Your 30-day continuous improvement challenge
Still reading? Good. Here’s your challenge:
Week 1: Document one broken process. Just one. Make it visible to everyone involved.
Week 2: Ask the people doing the work for three improvement ideas. Pick the easiest one.
Week 3: Implement that improvement. Measure the impact. Share the results.
Week 4: Do it again with another process.
That’s it. No consultants, no certifications, no complex software (unless you want it).
A retail chain tried this with their returns process. Month 1 saved 5 minutes per return. By month 6, they’d reduced return processing time by 65% and discovered $200,000 in process improvements.
The honest truth about getting started
Look, I could write another 5,000 words about methodologies and frameworks. But here’s what actually matters:
Your processes are broken. Your employees know how to fix them. The only question is whether you’ll create a system to capture and implement their ideas.
You could keep doing what you’re doing—losing money to inefficiency, frustrating employees with broken processes, and wondering why nothing improves.
Or you could start fixing things. One small improvement at a time.
The best part? You can start tomorrow. Pick your most annoying process. Ask people how to fix it. Then actually fix it.
Want to see how other mid-size companies make continuous improvement actually work without the complexity? Let’s have a real conversation about what’s broken in your workflows and how teams like yours fix them.
Frequently asked questions about continuous improvement
What is the difference between continuous improvement and continuous development?
Continuous improvement focuses on making existing processes better—fixing what’s broken, eliminating waste, speeding things up. Continuous development is about building new capabilities and skills. Think of it this way: improvement makes your car run better, development teaches you to fly a plane. Most companies need both, but improvement usually gives faster returns.
How do you measure the success of continuous improvement initiatives?
Forget complex KPIs. Track three things: cycle time (is work getting done faster?), error rate (are mistakes decreasing?), and satisfaction scores (are people happier?). A medical device company tracked just these three metrics and improved efficiency by 34% in one year. If you’re tracking 20 different metrics, you’re tracking nothing.
What’s the first step in implementing continuous improvement?
Start with the problem everyone complains about at lunch. Seriously. That recurring frustration everyone mentions? Fix that first. Don’t overthink it. A logistics company started by fixing their terrible coffee machine—sounds stupid, but it showed employees that management actually listened. Suggestion rate increased 400% after that.
Can continuous improvement work in creative or service industries?
Absolutely. A design agency reduced project delivery time from 6 weeks to 3 weeks by improving their revision process. A law firm cut document preparation time by 60% by creating templates based on paralegal feedback. Creativity isn’t chaos—even artistic work has processes that can improve.
How long does it take to see results from continuous improvement?
You can see initial results in days, not months. A restaurant fixed their order mix-up problem in one week by changing how orders display on kitchen screens. 50% reduction in wrong orders immediately. Big transformations take longer, but quick wins should happen fast or you’re doing it wrong.
What’s the biggest mistake companies make with continuous improvement?
Trying to fix everything at once. Companies launch 15 improvement initiatives simultaneously, overwhelm everyone, and nothing actually improves. One improvement done well beats ten improvements done poorly. A insurance company failed with their “transform everything” approach, then succeeded by fixing one process per month.
Do you need special software for continuous improvement?
No, but the right tools help you scale beyond sticky notes. You need three things: visibility into how work flows, a way for workers to suggest improvements where they work, and simple tracking of what’s getting better. Whether that’s software or a whiteboard depends on your size and complexity.
How do you get buy-in from skeptical employees?
Don’t sell them on “continuous improvement.” Just fix something they hate. When the printer that jams every day suddenly works, people notice. When the form that takes 20 minutes drops to 5 minutes, people care. Let results create believers, not PowerPoints about methodology.
What if our processes are regulated and can’t change?
Even regulated processes have flexibility in how they’re executed. A pharmaceutical company couldn’t change what they documented (FDA rules) but they could change how they documented it. Digital forms with auto-population cut documentation time by 70% while improving compliance. The regulation says what, not how.
Should we hire consultants for continuous improvement?
Consultants can help, but they can’t do it for you. Your employees know the problems and usually know the solutions. What they lack is permission and process to implement changes. Before hiring consultants, try giving your team authority to fix things. Often that’s all you need.
How is AI changing continuous improvement?
AI helps identify patterns humans miss. It can analyze thousands of process runs and spot bottlenecks instantly. But AI doesn’t fix processes—people do. A distribution center uses AI to predict delays, but warehouse workers still provide the insights on why delays happen and how to prevent them. AI is a tool, not a solution.
What’s the ROI of continuous improvement?
McKinsey found companies with mature continuous improvement programs show 23% higher profitability. But forget industry averages—track your own numbers. A small manufacturer invested $50,000 in improvement initiatives and saved $400,000 in the first year. That’s 8x ROI. Your results depend on how broken your processes are and how committed you are to fixing them.